Unter dem Motto „We automate molds“ präsentiert die ZAHORANSKY Automation & Molds GmbH auf der Fakuma 2024 in Friedrichshafen ihre Komplettlösungen für Fertigungsanlagen von Medizinprodukten auf Kunststoffbasis. Ob Primärverpackungen wie Fertigspritzen oder Vials, Systeme zur Verabreichung von Medikamenten oder Dialysezubehör: Basierend auf jahrzehntelanger Erfahrung in den Bereichen Maschinen- und Formenbau, Kunststofftechnik sowie Automation bietet ZAHORANSKY seinen Kunden umfassende Lösungen für die Fertigung komplexer Kunststoff-, Hybrid- und Glasersatzprodukte. Während Hersteller sonst häufig mit verschiedenen Maschinen- und Formenbauern sowie weiteren Dienstleistern zusammenarbeiten und ihre Produktionsanlage selbst zusammenstellen müssen, erhalten sie bei ZAHORANSKY alles aus einer Hand – von der Beratung und dem Produktdesign über die Entwicklung und Herstellung der Spritzgießwerkzeuge bis hin zur Konzeption und Installation hochautomatisierter No-Human-Touch-Fertigungsanlagen in Modulbauweise. Besucherinnen und Besucher der Fakuma erfahren auf dem Messestand (Halle A2, Stand 2309), wie sich dadurch mehr Umsetzungs-, Planungs- und Prozesssicherheit erreichen, die Gesamtanlageneffektivität steigern und Stückkosten sowie Personal- und Ressourceneinsatz minimieren lassen.
Jüngstes Beispiel ist eine von ZAHORANSKY entwickelte Automationslösung inklusive einer Innovation im Bereich des internen Werkzeughandlings für den Zwei-Komponenten-Spritzguss von Applikator-Verschlusskappen für digitale Diabetes-Sensoren. Die kompakte Anlage führt durch die minimale Werkzeugöffnung und einen hohen Automatisierungsgrad zu mehr Output und Prozesssicherheit bei deutlicher Platz- und Kosteneinsparung.
Bei der Realisierung der kundenspezifische Lösung für die hochautomatisierte Produktion von Applikator-Verschlusskappen im Zwei-Komponenten-Spritzgießverfahren, stellte nicht nur das Schraubgewinde der Kappe eine Herausforderungen dar – diese muss entspindelt werden, statt sie einfach aus dem Werkzeug auszustoßen. Aufgrund der beengten Platzverhältnisse wünschte sich der Kunde zudem eine kompakte Anlage mit hohem Automatisierungsgrad für die Serienproduktion großer Stückzahlen. Für diese individuelle Kundenlösung setzte ZAHORANSKY auf das Werkzeug Z.WARP move mit einer Innovation beim so genannten internen Werkzeughandling: Während die fertig gespritzte Grundkomponente mit einer werkzeugintegrierten automatischen Handlingeinheit entnommen wird, kann das Stichmaß verdichtet werden, bevor das Halbzeug für das Einspritzen der zweiten Komponente eingesetzt wird. Auf diese Weise werden die Abstände zwischen den Kavitäten für den weiteren Spritzgießprozess optimal eingestellt. Die anschließende Entnahme der fertigen Kappen erfolgt parallel zum Spritzgießen durch einen Sechs-Achs-Roboter. Das innovative Verfahren bietet dem Kunden eine Reihe von Vorteilen: Neben einer deutlich kürzeren Zykluszeit führt die minimale Werkzeugöffnung zu signifikanten Platz- und Kosteneinsparungen – auch da die zugehörige Spritzgießmaschine aufgrund der durchdachten Konstruktion ebenfalls wesentlich kleiner und damit günstiger ausfallen kann.
Zusätzlich kommt das Automationsmodul Z.SIROC für die Qualitätskontrolle zum Einsatz: Die fertigen Kappen werden vom Sechs-Achs-Roboter direkt in der Automationszelle zur Kamera geführt, dort vermessen, geprüft und gegebenenfalls aussortiert oder zur Weiterverarbeitung ausgegeben. Dies minimiert den Aufwand für Mitarbeitende und zudem stellt das Maschinenkonzept sicher, dass Gut- und Schlechtteile nicht vermischt werden.
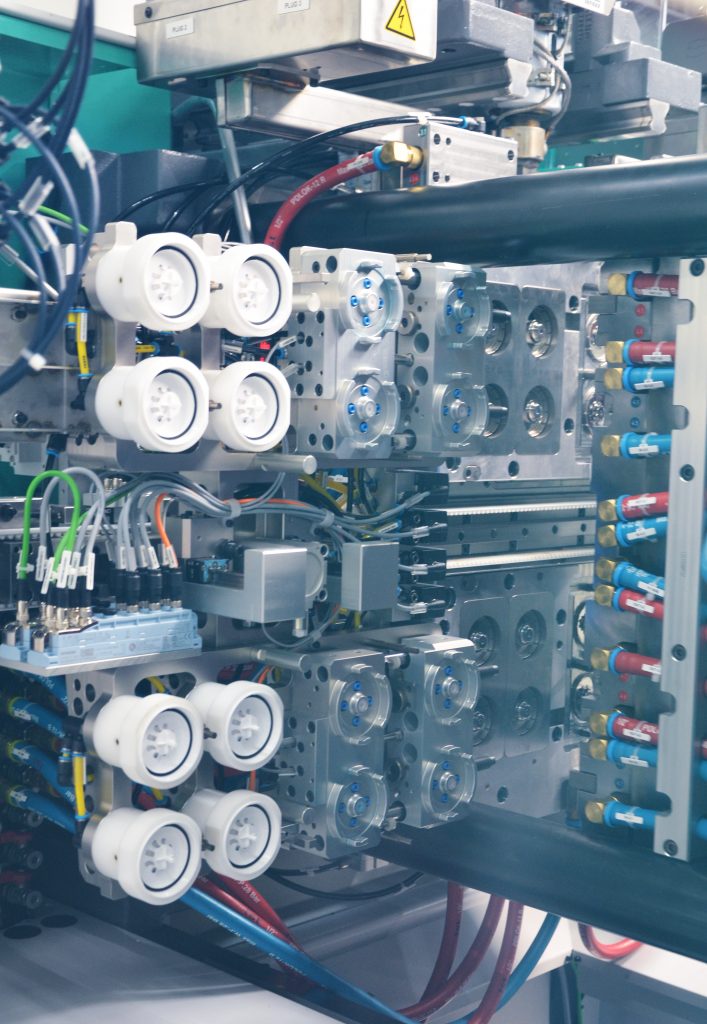
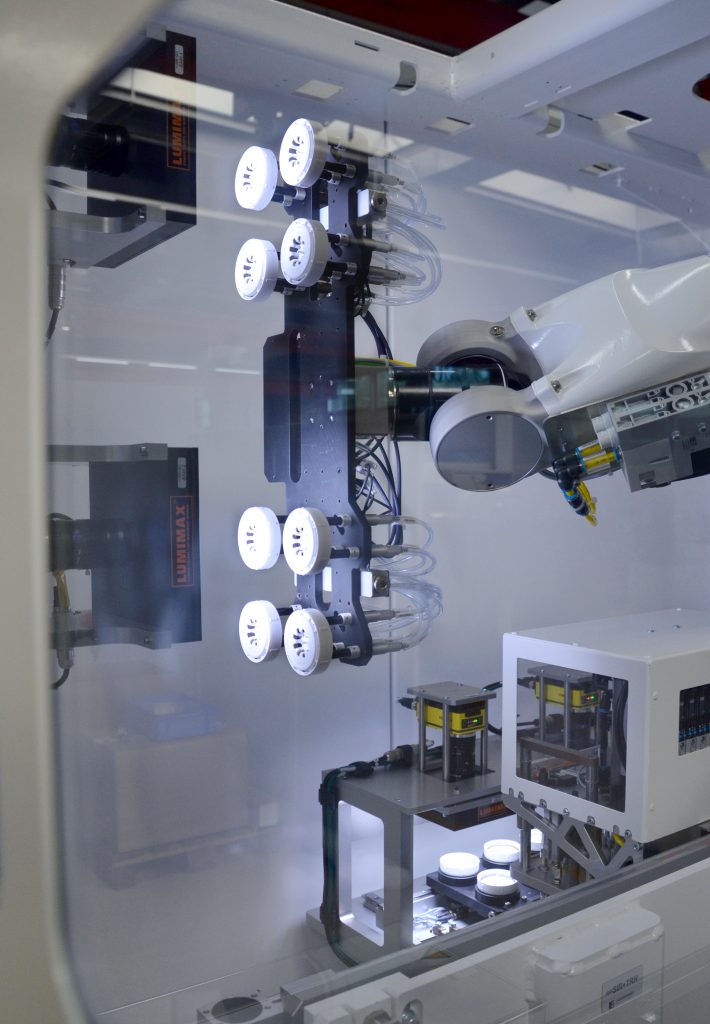