When it comes to our toothbrush-producing machines and systems, we go above and beyond the industry standard: In the form of automated large-scale systems, we will supply you with everything you need, from granules to pre-packaged and palletized toothbrushes – all fully automated and from a single source, and, as always, tailored perfectly to suit your needs. We call this concept the “one-stop solution“. The reaction it elicits from our customers can usually be summed up in one word: “wow!“.
Our large-scale systems are characterized by their greatest possible ease of operation and efficiency of processes, no matter the complexity of their structure: just a single operator will be able to monitor and control all production processes – without any manual intervention. This high level of full automation is only possible as a result of our ability to combine several modules from system technology, mold making, and plant construction like building blocks: injection molding, production, assembly, and packaging are carried out in one automated operation. In addition, all functions are displayed on the ZAHORANSKY Human Machine Interface (HMI) – even those of third-party modules! This ensures transparency at every stage of production and minimizes operating effort.
Benefits of a ZAHORANSKY large-scale system:
- Everything from a single source (one-stop solution) and turnkey implementation
- SPoC (single point of contact) with certified project managers (IPMA)
- End-to-end automation
- No manual intervention required thanks to full automation
- Modular design
- Automatic camera monitoring for the highest possible degree of process reliability
- Increased productivity with Overall Equipment Effectiveness (OEE) of up to 85 percent
- Fast and easy access for maintenance work
- 100% quality control for every single process, giving you an “OK parts” rate of 100%
- Preliminary process simulation to help identify bottlenecks and weak points
- Market-leading output of up to 40 parts per minute
We work in a customer-oriented way
One of our customers approached us with a conceptual idea for a new premium electric toothbrush. Conventional thinking dictates that two injection molding machines would be necessary to make this idea a reality. However, we went in a different direction, and suggested using only one of these machines in combination with integrated ZAHORANSKY modules and third-party modules. This concept brought several benefits and positive effects and was immediately met with approval: Although the system was slightly more complex in terms of its structure, it took up less space in the assembly hall – which, essentially, was exactly what the customer was looking for.
Another important aspect was the increased process reliability. The product could now be manufactured more easily, as all process steps – from injection molding, production and assembly, right through to packaging – were carried out in one system, fully automated and with 100% quality assurance. There were also a number of additional arguments in favor of this concept: as the large-scale system had many identical components (common parts), the stock of spare parts could be simplified significantly on the customer’s end. In connection with the easier accessibility during maintenance work, this resulted in reduced efforts in this area – the high machine availability of up to 85 percent played a not inconsiderable role in this regard. With details such as the use of several grinding wheels for a degree of rounding of over 95% for the individual filaments, we also ensured that, even at a high output of up to 40 toothbrushes/min., the product quality was still to an expected standard.
Typical fully automated manufacturing process of an electric toothbrush
At the very beginning of the process, the filaments are rounded in the ZAHORANSKY HanK Grinding Unit. Then, in the Z.AERO unit, mold bars are filled through the 3D tufting process, thus determining the perforated field geometry and topography that will come later. After the rear welding to secure the individual filament bundles, the mold bars are transported to the injection molding machine for overmolding – this is where the subsequent insertion of the mold bars is carried out by a six-axis robot. The basic brush head is now finished. Then, in the Final Brush Inspection (FBI) module, a 100 percent quality inspection is carried out by means of various camera systems. In addition, further optical controls are integrated between the individual process steps, which consistently guarantee that only 100 percent of good brush heads are used in the production process. All defect-free brush heads are now stored seamlessly in trays by a six-axis robot in the ZAHORANSKY Tray Loader Z.LODOS. By integrating the tray loader, the process is decoupled before further processing takes place. This is done primarily to increase the OEE accordingly.
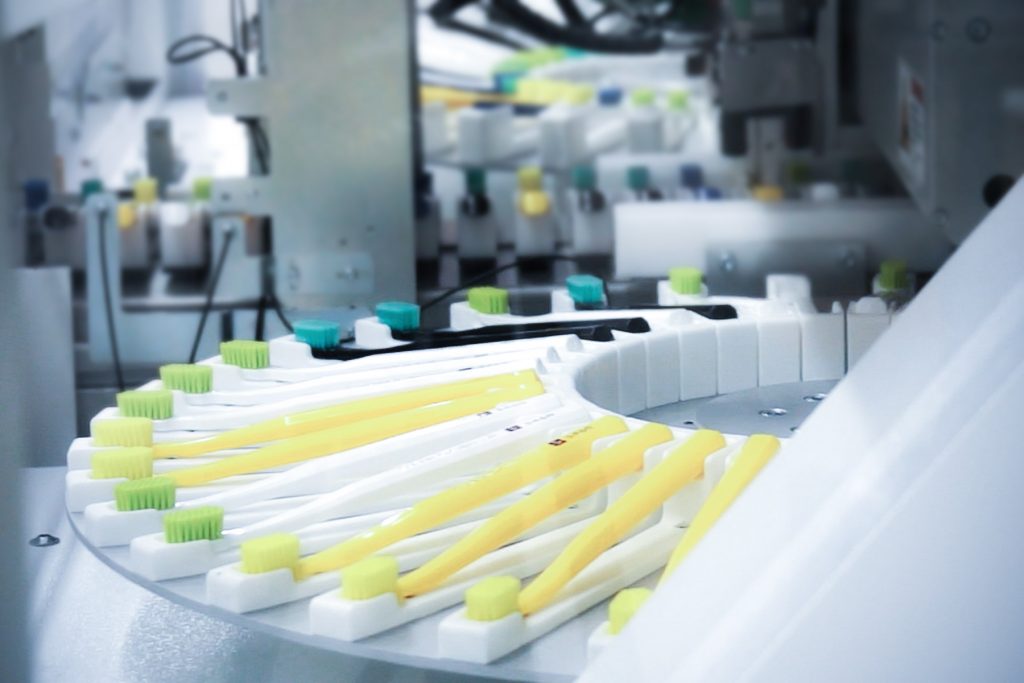
In the next step, the brush heads are removed from the ZAHORANSKY Tray Unloader and fed into the further assembly process. For this purpose, further components required for an electric toothbrush to function are mounted in the Z.MISTRAL unit across several assembly steps. Lastly, a number of coding and printing steps are carried out. In between each step, camera control systems are always checking to ensure the correct assembly process. After the protective caps have been mounted, the fully assembled brush heads are again shock-mounted in trays in a process that is fully automated, before they are blister packed in Z.PACK packaging machines.
Transfer of know-how into existing systems
Our experience in large-scale plant engineering will also be of benefit to you when it comes to existing manufacturing processes that relate to injection molding. For example, automated feed systems and packaging machines can increase production efficiency in upstream and downstream work stages.
We look forward to speaking with you and would like to invite you to pay a non-binding visit to our companies. Come and be blown away by the way we work and what we can offer you: Put us up to the challenge and we will give your large-scale systems the “wow!” factor and more!