Vaccines are provided in small vials which must meet strict quality specifications to ensure integrity, efficacy and patient safety. In a plant that produces vaccine vials, several image processing systems ensure that all quality criteria are met. Visuelle Technik GmbH integrated several Cognex image processing systems for quality assurance in a ZAHORANSKY production line for plastic vials.
Due to the covid pandemic, there has been an increasing focus on vaccines in recent years. ZAHORANSKY takes a different approach to producing vaccine containers than the usual one, explains Berthold Schopferer, Head of Project Planning at ZAHORANSKY, based in Freiburg, Germany: “Our injection molding and automation solution molds the containers from plastic in the clean room and assembles the TPE closure aseptically without any intermediate stations. In addition, we use special design measures to ensure that contamination is excluded.”
Automating defect detection with reliable, industry proven vision solutions
In order to check vaccine containers for compliance with industry specifications and to ensure that only defect-free vials are filled with vaccine, the ZAHORANSKY engineering team turned to Visuelle Technik GmbH, with whom they had previously implemented a number of systems for inspecting syringes with suitable vision systems.
Testing from four sides ensures completeness of inspection
The goal of the vision solution was to detect injection and cosmetic defects, such as air inclusions, mist in the material, small particles debris, surface scratches, over-molding, under-molding, deformations, flow lines, and others. These defects, which can be as small as a few µm, are reliably detected on the component, and defective vials are removed from the process. For this task, the team at Visuelle Technik GmbH developed a solution with their team that consists of four stations.
“At the first station, the vials are inspected from above. The area of interest here is the top edge of the vials, on which the cap is later placed and which must be free of defects to ensure that the containers are leak-proof,” says Sebastian Paschun, managing director of Visuelle Technik. “The second station gauges the complete side view of the vials, checking the height, width, and various other dimensions. To check the entire shell surface in the side view, the third station works with a line-scan camera in front of which the vials are rotated. Here, an illumination concept developed by Visuelle Technik and physically implemented by ZAHORANSKY is used. Finally, the bottom of the containers is inspected at the fourth station.”
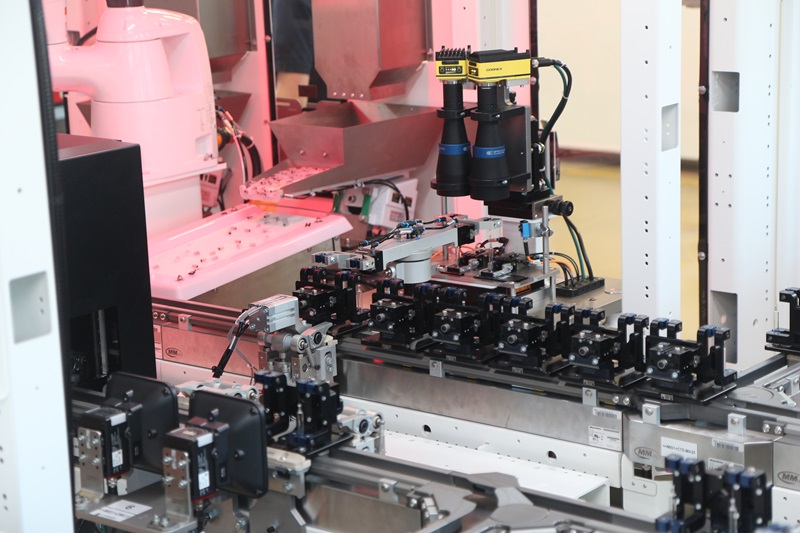
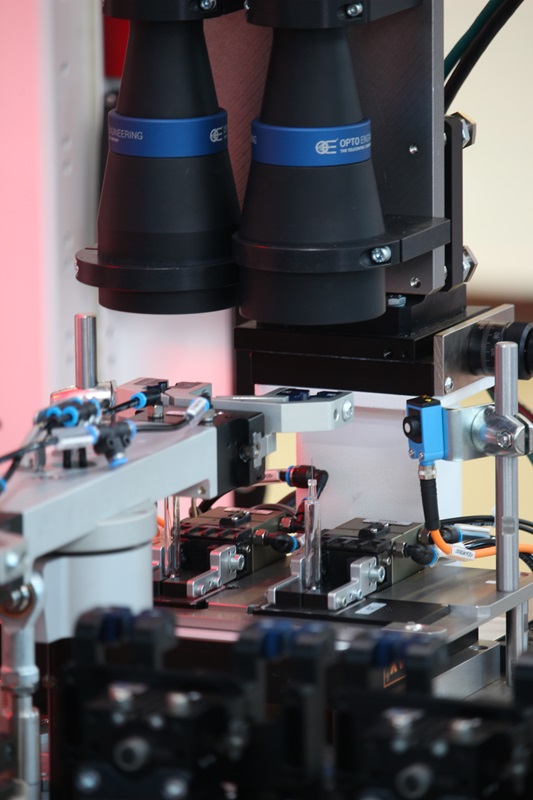
Multi-camera solution offers greater coverage and higher resolution imaging
Visuelle Technik was under great time pressure, recalls Paschun: “Due to the acute demand for vials, ZAHORANSKY’s requirement was to get the inspection systems deployed into production as quickly as possible. At this point, our experience from the systems we had previously developed for ZAHORANSKY paid off. Due to the short time available, we adapted the existing, robust concepts to the new requirements and were thus able to implement this project successfully and within the tight deadline.”
According to Paschun, a critical factor in this performance were the vision systems from Cognex: (4) In-Sight 9902 line scan cameras and (6) In-Sight 9912 area scan cameras are used in each of the ten production lines. Visuelle Technik selected these models due to their easy integration into the ZAHORANSKY lines, problem-free integration into the existing Profinet network, and their ease of use and maintenance. “In addition, the In-Sight 9902 and 9912 with resolutions of 2,000 pixels per line and 12 megapixels, respectively, enable optimal conditions for highly accurate inspection performance, coupled with fast processing times. For the end customer, these smart cameras also offer the advantage of a modular design and thus enable extensions or a reduction in the number of cameras used if required.
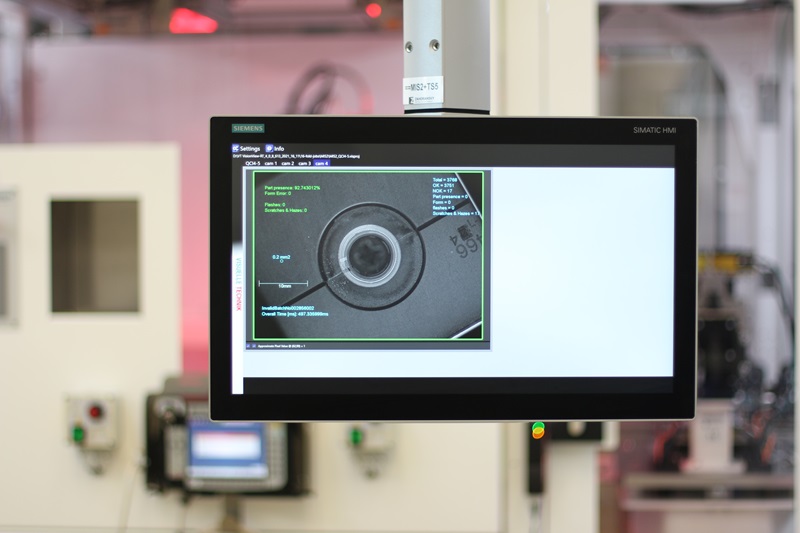
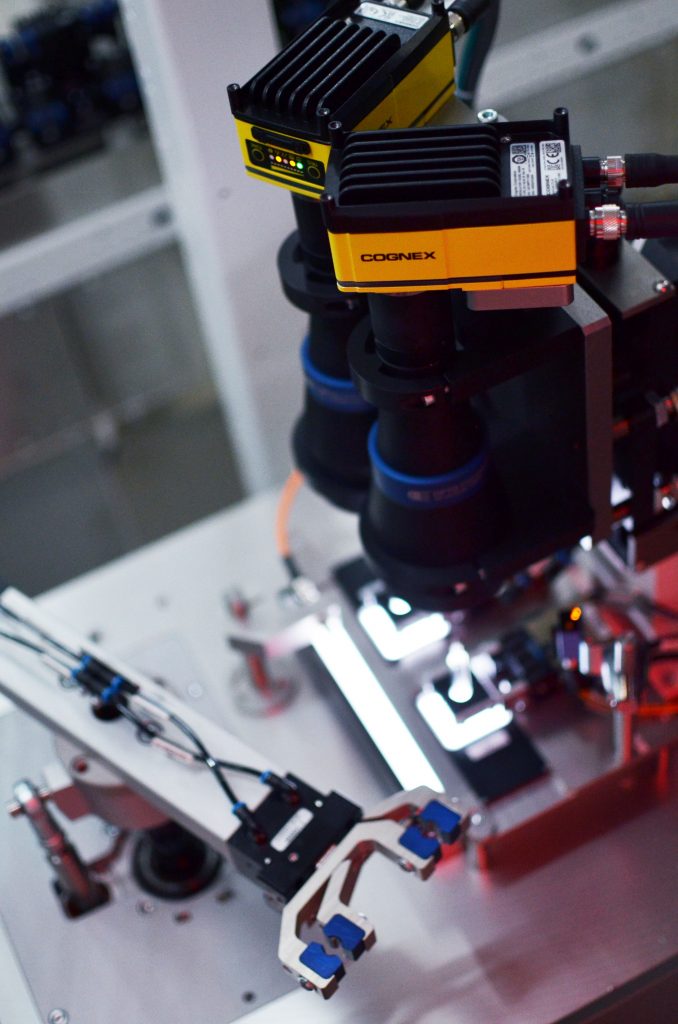
Around the clock coverage with precise results and fewer false defects
The ten fully automated lines have been running at the end customer’s site for many months at a machine rate of around 30 parts per minute and can produce vials in four different sizes of 2 ml, 6 ml, 10 m,l and 20 ml continuously, seven days a week, if required. “Our customer has reported back to us that they are extremely satisfied with the lines as well as the defect detection and they have been able to significantly reduce their rate of false defect,” says ZAHORANSKY application engineer Andreas Kirstein. “The vision systems from Cognex and the precise implementation by Visuelle Technik have played a crucial role in this success.”
The original article created and published by Cognex can be found here: https://www.cognex.com/customer-stories/pharmaceuticals/vial-inspection-ensures-product-integrity-and-patient-safety