Impfstoffe gegen Covid und andere Krankheiten werden in kleinen Fläschchen, so genannten Vials bereitgestellt, die zur Sicherheit der Patienten strengen Qualitätsvorgaben entsprechen müssen. In einer ZAHORANSKY-Anlage für die Produktion von Kunststoff-Vials integrierte die Visuelle Technik GmbH zur Qualitätssicherung mehrere Bildverarbeitungssysteme von Cognex.
Die Bilder von Medikamentencontainern für flüssige Impfstoffe sind aufgrund der Covid-Pandemie in den vergangenen Jahren mehr als je zuvor in den Mittelpunkt des allgemeinen Bewusstseins gerückt. Vials bestehen in der Regel aus Glas und werden nach der Abfüllung des Impfstoffs mit einem Stopfen aus einem thermoplastischen Elastomer (TPE) und einer Bördelkappe aus Aluminium verschlossen. Glas als Material für diese Impfstofffläschchen bringt jedoch einige Nachteile mit sich: Die Behälter müssen nach ihrer Produktion kostenintensiv gereinigt und sterilisiert werden, bevor sie befüllt werden können. Zudem bergen sie die Gefahr von Splittern bei Glasbruch.
ZAHORANSKY geht bei der Produktion solcher Medikamentencontainer einen anderen Weg, erläutert Berthold Schopferer, Head of Project Planning des in Freiburg ansässigen Unternehmens: „Unsere Spritzgieß- und Automatisierungslösung spritzt die Behälter im Reinraum aus Kunststoff und montiert den TPE-Verschluss aseptisch ohne jegliche Zwischenstation. Die dabei eingesetzten Roboter und die Spritzgießform erfüllen die Anforderungen des Reinraums Klasse 5. Zudem stellen wir mit besonderen konstruktiven Maßnahmen sicher, dass Verunreinigungen durch Partikel ausgeschlossen werden.“ Der große Vorteil gegenüber gläsernen Impfstoffbehältern besteht laut Bertold Schopferer darin, dass auf diese Weise keine Sterilisierung mehr erforderlich ist. Die Arbeitsgänge Waschen, Trocknen, Prüfen und Sterilisieren entfallen somit, was zu erheblichen Kosteneinsparungen führt.
Optimiert für Variationen
Die Verwendung von Kunststoff als Basis für die Behälter führt jedoch zu anderen Herausforderungen, die das Entwicklungs-Team von ZAHORANSKY bewältigen musste. So weisen produzierte Fläschchen aus diesem Material eine deutlich höhere Variation auf als Glas-Container. Um ausnahmslos alle gefertigten Impfstoff-Behälter auf Einhaltung der Spezifikationen zu prüfen und sicherzustellen, dass nur fehlerfreie Vials mit Impfstoff befüllt werden, wandten sich die ZAHORANSKY-Ingenieure an die Visuelle Technik GmbH, mit der sie zuvor bereits einige Anlagen zur Prüfung von Syringen mit Hilfe geeigneter Bildverarbeitungssysteme umgesetzt hatten.
„Mit diesem Partner hatten wir in der Vergangenheit schon viele positive Erfahrungen gemacht und wussten, dass wir uns auf die vorhandene Expertise rund um die Bildverarbeitung verlassen können“, berichtet Andreas Kirstein, ZAHORANSKY-Application Engineer – Vision System. „Zudem ist die Visuelle Technik GmbH seit Jahren Teil des innovativen PSI-Netzwerks von Cognex und somit ein bevorzugter Partner für die Integration von Bildverarbeitungssystemen in Anlagen, die in verschiedensten Branchen zum Einsatz kommen. Wir waren uns sicher, dass es im Cognex-Portfolio auch für unsere aktuelle Aufgabenstellung die richtige Lösung gibt.“
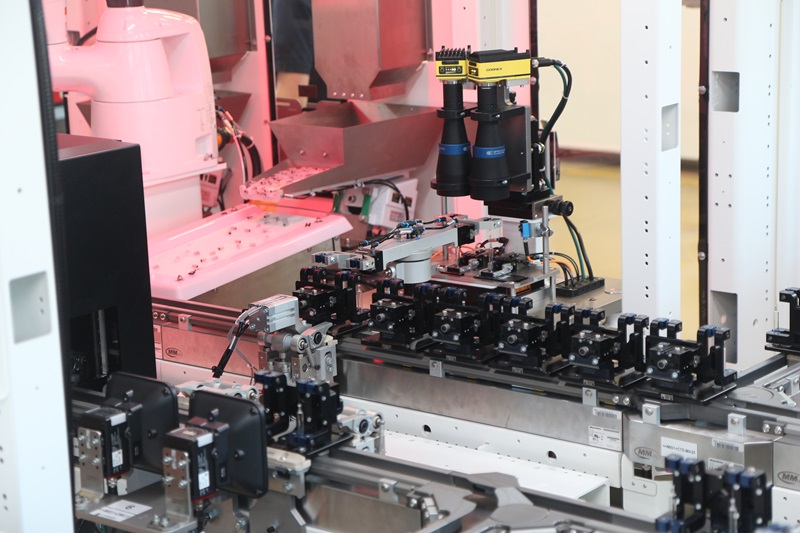
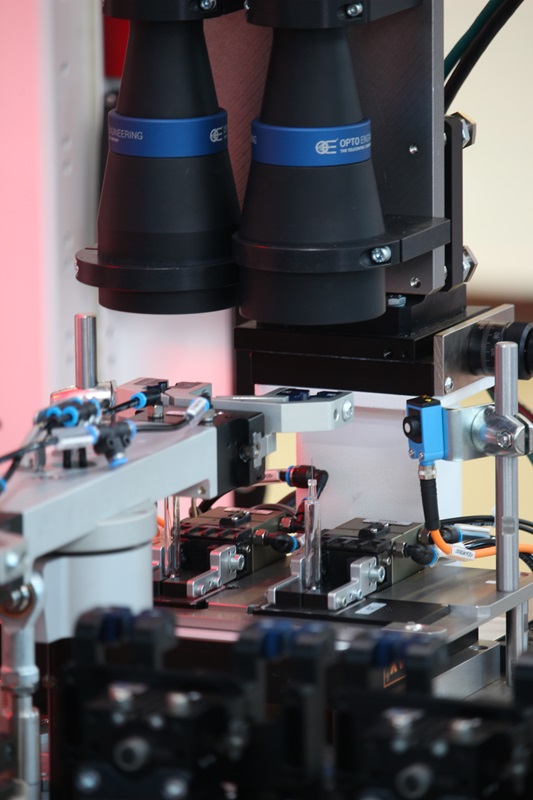
Prüfung von vier Seiten
Ziel der Bildverarbeitungslösung war es, Spritzfehler und kosmetische Defekte zu erkennen. Hierzu zählen Lufteinschlüsse, Nebel im Material, Black Specs (kleinste Partikel), Einschlüsse im Kunststoff, Kratzer, Überspritzungen, Unterspritzungen, Ausbrüche, Deformationen, Fließlinien und andere. Diese Fehler werden ab Größen im Bereich von wenigen µm am gesamten Bauteil sicher erkannt und fehlerhafte Vials durch eine geeignete Kommunikation mit der Anlage aus dem Prozess genommen. Für diese Aufgabe entwickelten Sebastian Paschun und Meinrad Borho, beide Geschäftsführer der Visuelle Technik GmbH, mit ihrem Team eine Lösung, die aus vier Stationen besteht.
„An der ersten Station werden die Vials von oben geprüft. Entscheidend ist hierbei der oberste Rand der Fläschchen, auf dem später der Verschlussdeckel aufgesetzt wird und der fehlerfrei sein muss, um die Dichtheit der Behälter zu gewährleisten“, so Sebastian Paschun. „Die zweite Station vermisst die komplette Seitenansicht der Vials und kontrolliert dabei die Höhe, die Breite und diverse andere Maße. Um die gesamte Mantelfläche in der Seitenansicht prüfen zu können, arbeitet die dritte Station mit einer Zeilenkamera, vor der die Vials gedreht werden. Hierbei kommt ein durch Visuelle Technik entwickeltes und von ZAHORANSKY konstruktiv umgesetztes Beleuchtungskonzept zum Einsatz. Der Boden der Behälter wird schließlich an der vierten Station inspiziert.“
Zehn Kameras pro Anlage
Für die Realisierung der gesamten Bildverarbeitungslösung stand Visuelle Technik unter großem Zeitdruck, erinnert sich Paschun: „Aufgrund des akuten Bedarfs an Vials war die Vorgabe von ZAHORANSKY, die Anlagen schnellstmöglich in die Produktion zu bekommen. An dieser Stelle machten sich unsere Erfahrungen aus den Anlagen bezahlt, die wir schon früher für ZAHORANSKY entwickelt hatten: Wir haben die dafür bestehenden, robusten Konzepte auf Grund der knappen Zeit fast nur in der Theorie an die neuen Bedürfnisse angepasst und konnten dieses Projekt dadurch erfolgreich und innerhalb der knappen Zeitvorgabe umsetzen.“
Ein entscheidender Faktor für diese Leistung waren laut Paschun die Bildverarbeitungssysteme von Cognex: In jeder der mittlerweile realisierten zehn Produktionslinien sind vier intelligente Zeilenkamerasysteme vom Typ In-Sight 9902 und sechs Flächenkamerasysteme vom Typ In-Sight 9912 im Einsatz. Diese Modelle überzeugten Visuelle Technik unter anderem durch ihre einfache Integration in die ZAHORANSKY-Anlagen, die problemlose Einbindung in das vorhandene Profinet-Netzwerk sowie ihre Benutzer- und Wartungsfreundlichkeit. „Zudem ermöglichen die In-Sight 9902 und 9912 mit Auflösungen von 2000 Pixeln pro Zeile bzw. 12 Megapixeln die optimalen Voraussetzungen für eine hochgenaue Inspektionsleistung und überzeugen durch konstante Auswertezeiten. Für den Endkunden bieten diese Smart-Kameras außerdem den Vorteil, dass sie einen modularen Aufbau des Gesamtsystems und dadurch bei Bedarf Erweiterungen oder eine Reduzierung der eingesetzten Kameras ermöglichen.
Bei der Validierung der Kameras vertrauten sowohl der Endkunde als auch ZAHORANSKY auf das langjährige Know-how von Visuelle Technik: „Der Endkunde hatte zunächst keine konkreten Vorstellungen davon, wie gut die von uns vorgeschlagenen Kameras Defekte erkennen können. Nach der Inbetriebnahme der ersten Anlage mit dieser Bildverarbeitungs-Ausstattung bemerkte er damit Fehler, die er zuvor gar nicht kannte“, so Paschun. Dies führte dazu, dass die ursprünglichen Anforderungen an das System in Bezug auf die Fehlergröße während der Inbetriebnahme der Kameras von einer Fläche von 0,2 mm2 auf 0,02 mm2 geändert wurden. Die Entwickler von Visuelle Technik konnten diese angepassten, anspruchsvolleren Spezifikationen durch eine Optimierung der Algorithmik ohne Änderungen der Hardware in kürzester Zeit umsetzen.
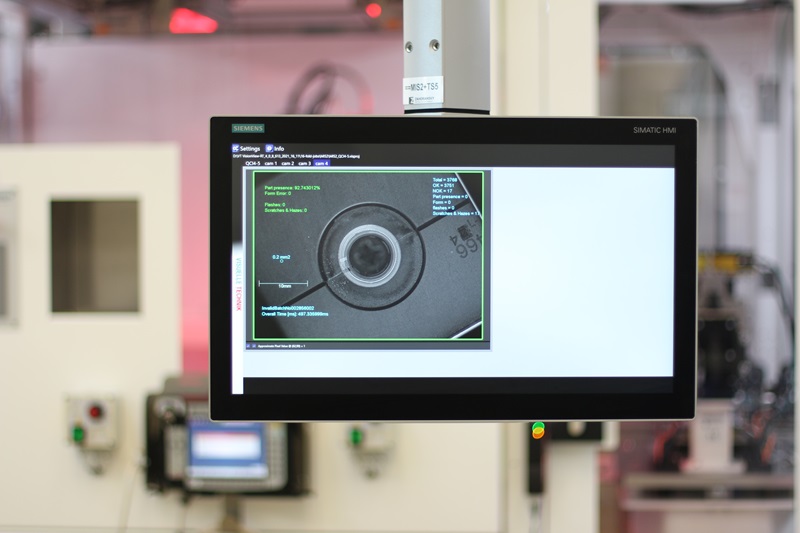
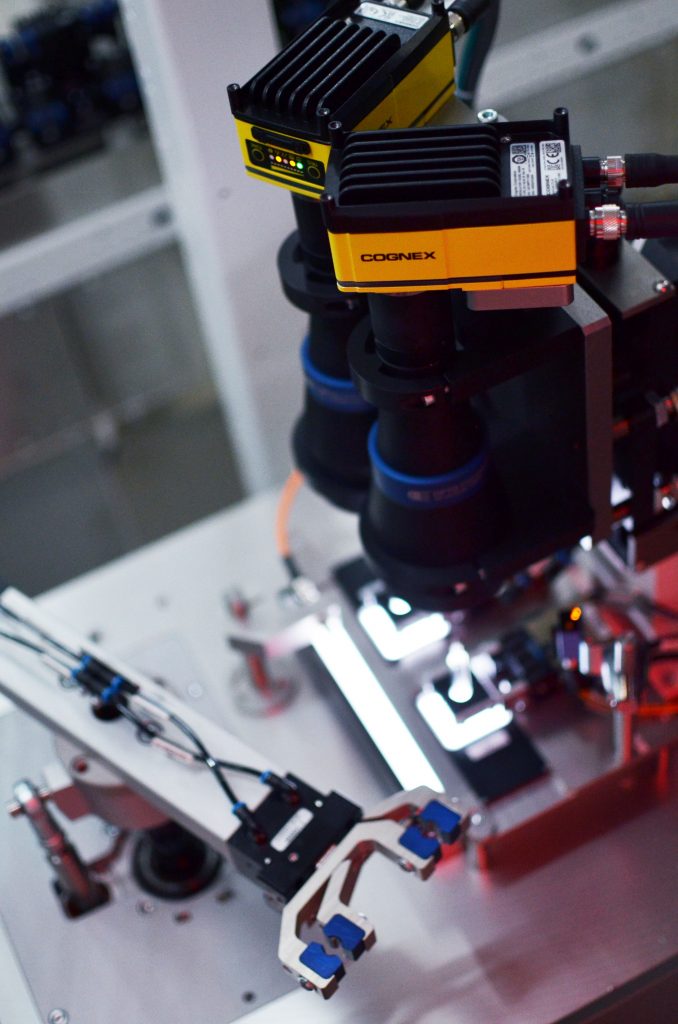
Qualität rund um die Uhr
Die zehn vollautomatisierten Anlagen laufen beim Endkunden seit vielen Monaten mit einem Maschinentakt von ca. 30 Teilen pro Minute und können bei Bedarf Vials in vier unterschiedlichen Größen mit 2 ml, 6 ml, 10 ml und 20 ml an sieben Tagen die Woche rund um die Uhr produzieren. „Unser Kunde hat uns zurückgemeldet, dass er mit den Anlagen sowie der Fehlererkennung äußerst zufrieden ist und seine Pseudoausschussrate deutlich reduzieren konnte“, freut sich ZAHORANSKY-Application Engineer – Vision System Andreas Kirstein über das positive Kunden-Feedback. „Die Bildverarbeitungssysteme von Cognex und die perfekte Umsetzung durch Visuelle Technik haben wesentlichen Anteil an diesem Erfolg.“
Den von Cognex erstellten und veröffentlichten Originalbeitrag finden Sie hier: https://www.cognex.com/customer-stories/pharmaceuticals/vial-inspection-ensures-product-integrity-and-patient-safety