Bei unseren Maschinen und Anlagen für die Produktion von Zahnbürsten gehen wir weit über den Branchenstandard hinaus: In Form automatisierter Großanlagen erhalten Sie bei uns vom Granulat bis zur fertig verpackten und palettierten Zahnbürsten alles aus einer Hand und voll automatisiert – wie immer perfekt abgestimmt auf Ihre Bedürfnisse. Wir nennen dieses Konzept „One-Stop-Solution“. Die Reaktion unserer Kunden darauf ist in der Regel kürzer: „Oh!“.
Unabhängig von der Komplexität des Aufbaus zeichnen sich unsere Großanlagen durch größtmögliche Einfachheit in der Bedienung und Effizienz in den Abläufen aus: Ein Bediener reicht aus, um sämtliche Produktionsprozesse zu überwachen und zu steuern – ohne manuell eingreifen zu müssen. Dieser hohe Grad der Vollautomatisierung ist nur deswegen möglich, weil wir mehrere Module aus der Systemtechnik, dem Formen- und Anlagenbau wie in einem Baukasten kombinieren können: Das Spritzgießen, die Herstellung bzw. Montage sowie Verpackung erfolgen automatisiert in einem Arbeitsgang. Darüber hinaus werden sämtliche Funktionen am ZAHORANSKY Human Machine Interface (HMI) angezeigt – auch diejenigen von Fremdbaugruppen! Das sorgt für Transparenz in jeder Phase der Produktion und minimiert jeglichen Bedienungsaufwand.
Vorteile einer ZAHORANSKY Großanlage
- Alles aus einer Hand (One-Stop-Solution) und Turn-Key-Abwicklung
- Single-point-of-contact über zertifizierte Projektleiter (IPMA)
- Durchgängige Automatisierung
- Keine manuellen Eingriffe notwendig dank Vollautomatisierung
- Modulare Bauweise
- Automatische Kameraüberwachung für bestmögliche Prozesssicherheit
- Gesteigerte Produktivität mit einer Maschinenverfügbarkeit (Overall Equipment Effectiveness, OEE) von bis zu 85 Prozent
- Einfacher und schneller Zugang für Wartungsarbeiten
- 100%ige Qualitätskontrolle über jeden einzelnen Prozess und damit 100 Prozent Gutteile
- Prozesssimulation im Vorfeld zur Identifikation von Bottle Necks und Schwachstellen
- Marktführender Output von bis zu 40 Teilen in der Minute
Wir arbeiten kundenorientiert
Einer unserer Kunden trat mit einer Konzeptidee für eine neue elektrische Premium-Zahnbürste an uns heran. Herkömmlich gedacht, wären dafür zwei Spritzgießmaschinen nötig gewesen. Wir schlugen stattdessen vor, nur eine in Verbindung mit weiteren integrierten ZAHORANSKY- und Fremd-Modulen zu verwenden. Dieses Konzept fand aufgrund mehrerer Vorteile und positiver Effekte sofort seine Zustimmung: Obwohl die Anlage vom Aufbau her etwas komplexer war, benötigte sie weniger Platz in der Montagehalle – was dem Kunden bereits grundsätzlich entgegenkam.
Einen weiteren wichtigen Aspekt stellte die gestiegene Prozesssicherheit dar. Das Produkt ließ sich nun einfacher herstellen, denn alle Prozessschritte, vom Spritzguss über die Herstellung und Montage bis zur Verpackung, liefen in einer Anlage ab – vollautomatisiert und mit 100%iger Qualitätskontrolle. Darüber hinaus sprachen weitere Argumente dafür: Da sich in der Großanlage viele identische Bauteile (Gleichteile) befanden, konnte die Ersatzteilhaltung kundenseitig deutlich vereinfacht werden. In Verbindung mit der einfacheren Zugänglichkeit bei Wartungsarbeiten ließen sich die Aufwände in diesem Bereich weiter reduzieren – die hohe Maschinenverfügbarkeit von bis zu 85 Prozent hatte daran einen nicht unerheblichen Anteil. Über Details wie die Verwendung mehrerer Schleifscheiben für eine mehr als 95%ige Verrundung der Einzelfilamente stellten wir darüber hinaus sicher, dass auch die Produktqualität bei hohem Output von bis zu 40 Zahnbürsten/Min. passt.
Vollautomatischer Herstellungsprozess einer elektrischen Zahnbürste
Ganz am Anfang steht die Verrundung der Filamente in der ZAHORANSKY HanK Grinding Unit. Danach werden in der Z.AERO Einheit im 3D-Tufting-Verfahren Moldbars befüllt und somit die spätere Lochfeldgeometrie und -topografie bestimmt. Nach dem rückseitigen Verschweißen zur Fixierung der einzelnen Filamentbündel werden die Moldbars an die Spritzgießmaschine zum Überspritzen transportiert, wobei das anschließende Einlegen der Moldbars durch einen Sechsachsroboter erfolgt. Jetzt ist der Grundbürstenkopf fertiggestellt. Danach erfolgt im Final Brush Inspection (FBI)-Modul die 100 Prozent Qualitätsüberprüfung durch diverse Kamerasysteme. Zusätzlich sind noch weitere optische Kontrollen zwischen den einzelnen Prozessschritten integriert, um durchgängig zu garantieren, dass nur 100 Prozent gute Bürstenköpfe im Prozess gehandhabt werden. Alle fehlerfreien Bürstenköpfe werden nun durch einen Sechsachsroboter lückenlos im ZAHORANSKY Tray Loader Z.LODOS in Trays abgelegt. Durch die Integration des Tray Loaders wird der Prozess vor der Weiterverarbeitung entkoppelt. Dies dient in erste Linie dazu, den OEE entsprechend zu erhöhen.
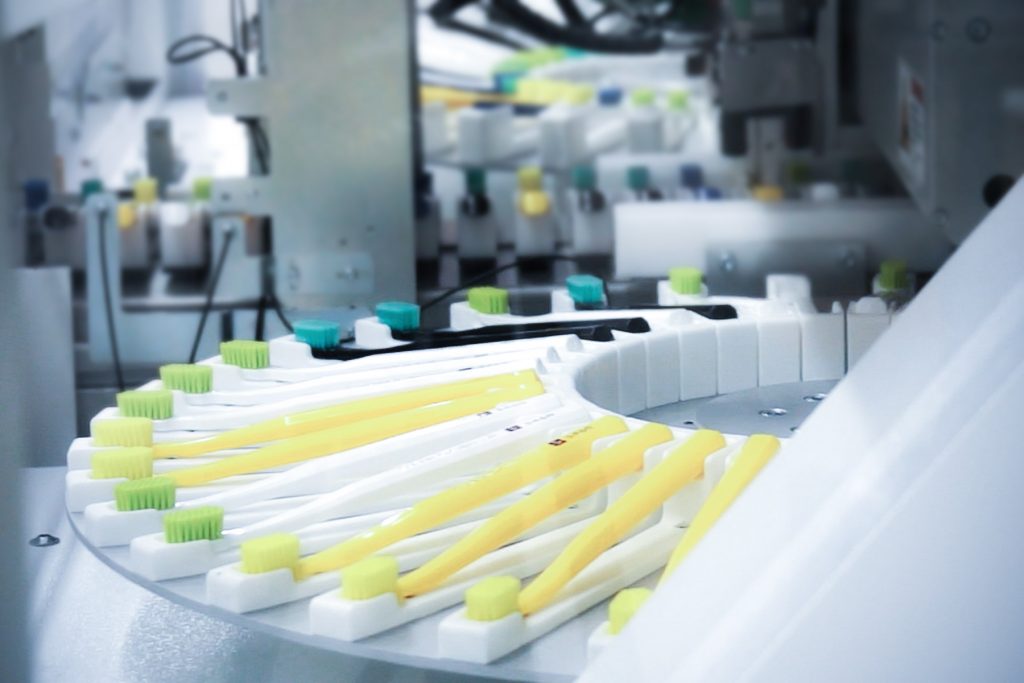
Im nächsten Schritt erfolgt die Entnahme der Bürstenköpfe im ZAHORANSKY Tray Unloader und deren Zuführung in den weiteren Montageprozess. Dazu werden in der Z.MISTRAL Unit in mehreren Montageschritten weitere der für die Funktion einer elektrischen Zahnbürste erforderlichen Bauteile montiert. Zu guter Letzt erfolgen diverse Kodierungs- und Bedruckungsschritte. Dazwischen sind immer wieder Kamerakontrollsysteme, um den korrekten Montageablauf zu gewährleisten. Nach der Schutzkappenmontage werden die fertig montierten Bürstenköpfe wieder vollautomatisch in Trays gepuffert, bevor sie dann den Blisterverpackungsprozess in Z.PACK Verpackungsmaschinen durchlaufen.
Know-how-Transfer in bestehende Anlagen
Unsere Erfahrungen aus dem Großanlagenbau kommen Ihnen auch bei bereits bestehenden spritzgießnahen Fertigungsprozessen zugute: Beispielsweise lässt sich über automatisierte Zuführsysteme und Verpackungsmaschinen die Produktionseffizienz in vor- und nachgelagerten Arbeitsschritten steigern.
Wir freuen uns auf den Dialog mit Ihnen und laden Sie gerne zu einem unverbindlichen Besuch unserer Firmen ein. Überzeugen Sie sich selbst davon, wie wir arbeiten und was wir Ihnen bieten können: Fordern Sie uns und wir liefern Ihnen mehr als ein „Oh!“ für Ihre GrOh!ßanlage!